¿QUÉ CAUSA LA FALLA DE LA PCB?
Ya sea una falla catastrófica o una falla de campo latente, nada es más frustrante y costoso que cuando una tarjeta de circuito deja de funcionar. Se creo el diseño del prototipo y se probó a fondo y, sin embargo, tiene problemas una vez que está en plena producción. ¡¿Qué es lo pasó?!
No puedo hablar de todos los posibles problemas de control de calidad que pueden colarse en un proceso de ensamblaje de la PCB, pero la contaminación sigue siendo un problema subyacente en muchos problemas de confiabilidad de la PCB. Hay esencialmente dos grandes categorías de contaminación por PCB, iónica y no iónica. En este artículo, nos concentraremos en gran medida en las fuentes de contaminación iónica
¿QUÉ ES LA CONTAMINACIÓN IÓNICA DE UNA PCB?
Los contaminantes iónicos son restos de flux que quedan durante el proceso de ensamblaje. Los compuestos iónicos se mantienen unidos por fuerzas electrostáticas: el compuesto en sí tiene una carga neta cero. Estas fuerzas electrostáticas están compuestas de cationes cargados positivamente y aniones cargados negativamente. Un ejemplo simple es la sal de mesa (cloruro de sodio), compuesta por un solo catión de sodio positivo (Na) al que le falta un electrón y un anión de cloruro (Cl) con carga negativa que tiene un electrón extra.
Al llenar la tarjeta con componentes, los componentes mismos también pueden llevar varios contaminantes iónicos/conductores a su ensamblaje, incluidos los aceites/líquidos de corte, biocidas y preventivos de corrosión. Tenga en cuenta los materiales no iónicos comunes que también pueden afectar los pasos de ensamblaje: aceites de proceso, desmoldantes, etc. Estos materiales no iónicos pueden ser perjudiciales en el futuro.
Las fuentes de contaminación pueden originarse en cualquier punto del proceso del ensamblaje, así que empecemos por el principio. Acaba de recibir un nuevo lote de tarjetas vacías que completará con los componentes necesarios para su producto.
CONTAMINANTES IÓNICOS COMUNES DE LA FABRICACIÓN DEL TARJETAS VACÍO
- La humedad común puede quedar atrapada en casi cualquier parte del proceso de las "capas". Esto conduce a la disociación de otros materiales iónicos, sentando así las bases para contratiempos conductivos (crecimiento dendrítico, ECM, etc.). Es una práctica común “hornear” las tarjetas para eliminar la humedad extraña.
Corrosión por contaminación en la fabricación de la PCB: cortesía de Foresite, Inc
- Productos químicos de grabado: estos son altamente conductivos y también pueden ser corrosivos. Deben neutralizarse químicamente y eliminarse/enjuagarse, y son conocidos como fuentes de fugas de corriente.
Residuos pesados de flux sin limpieza con corrosión visible del cobre, cortesía de Foresite, Inc.
Todo el mundo está familiarizado con los residuos de flux. Los fluxs, ya sea en forma líquida, de alambre con núcleo o compuestos como una pasta, pueden dejar residuos que pueden causar serios defectos de confiabilidad si no se eliminan. Los residuos de fluxs conductores comunes del proceso de soldadura pueden incluir varios activadores, aglutinantes, componentes de reológia y saponificadores que no han reaccionado. Entre estos se encuentran numerosas iteraciones de ácidos (abiético, adípico y succínico, entre otros), ingredientes altamente básicos (compuestos amino) e incluso constituyentes que se encuentran en "jabones", como iones de fosfato y sulfato. Todos estos contaminantes deben limpiarse del sustrato. Los procesos de limpieza incluyen una limpieza estricta con solventes, como el desengrasado con vapor, y productos químicos acuosos en los limpiadores comunes por lotes o en línea, como se ve en la planta de fabricación.
- Residuos entre capas: se pueden esparcir durante la perforación ya través de los procesos de enchapado.
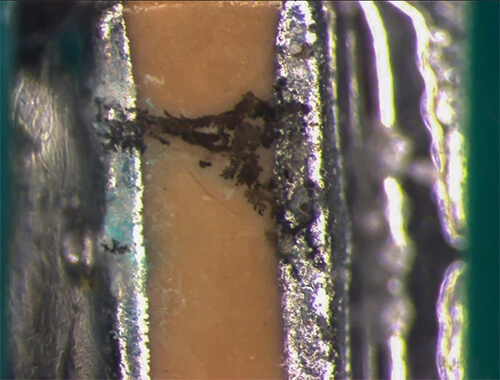
Crecimiento dendrítico entre las almohadillas de soldadura, causado por contaminación iónica, cortesía de Foresite, Inc.
Además de estos residuos que se encuentran comúnmente, también se deben eliminar los residuos de la química del proceso de limpieza. Estos residuos relacionados con la limpieza se notan más en los sistemas de limpieza acuosos. Muchos sistemas usan saponificadores para neutralizar y emulsionar los residuos de flux y hacerlos más fáciles de enjuagar/eliminar del sustrato. Estos componentes son altamente iónicos y también pueden mejorar el mecanismo de migración de dendritas y/o electroquímica (ECM) si no se eliminan. Además, los prohibidores de corrosión y los tensioactivos se emplean comúnmente en estos productos. Esto no es malo en sí mismo, pero se debe tener cuidado para garantizar que los protectores contra la corrosión y tensioactivos se eliminen junto con la suciedad durante el proceso de limpieza.
ReALIZAR PRUEBAS DE CONTAMINACIÓN IÓNICA PARA ENCONTRAR CONTAMINANTES
El control de calidad deficiente desde la fabricación de la tarjeta de circuito impresa, pasando por la soldadura y la población de componentes, hasta las etapas finales de limpieza, son fuentes potenciales de contaminación. Muchos de estos contaminantes se pueden encontrar mediante pruebas y análisis de contaminación iónica, como pruebas de resistividad del extracto de solvente (ECM), extracción de iones y cromatografía. También se pueden identificar durante las pruebas iniciales de validación de alta humedad al comienzo del proyecto.
El estricto control de calidad y los procedimientos operativos estándar durante el ensamblaje de la PCB, las etapas de fabricación del ensamblaje y las pruebas de validación pueden contribuir en gran medida a prevenir una falla. Solo piense: el simple manejo incorrecto de una pieza por parte de un operador que no usa guantes podría resultar en la transferencia de sales y aceites de la piel al sustrato. ¡Tal negligencia podría ser potencialmente catastrófica para su artículo!
Techspray ofrece una línea completa de removedores de flux que son altamente efectivos para eliminar la contaminación iónica antes de que provoque fallas en la tarjeta. El Removedor de flux G3 de Techspray es un poderoso solvente no inflamable que elimina los residuos sin esfuerzo.
El removedor de flux PWR-4 está diseñado para reemplazar solventes tóxicos, como el bromuro de n-propilo (nPB), que se usan comúnmente en desengrasadores de vapor y equipos ultrasónicos.
El removedor a base de agua Eco-der SMT200 está diseñado para limpiar tarjetas de circuitos electrónicos, incluso con metales sensibles, en un sistema de limpieza por lotes o en línea.
Para obtener más información, comuníquese con Techspray al 678-819-1408 o envíenos un mensaje aquí.